What is Porosity in Welding: Ideal Practices for Staying Clear Of Permeable Welds
What is Porosity in Welding: Ideal Practices for Staying Clear Of Permeable Welds
Blog Article
The Scientific Research Behind Porosity: A Comprehensive Guide for Welders and Fabricators
Comprehending the intricate mechanisms behind porosity in welding is important for welders and producers pursuing impeccable craftsmanship. As metalworkers explore the depths of this sensation, they discover a world regulated by different elements that influence the development of these tiny voids within welds. From the structure of the base products to the intricacies of the welding process itself, a multitude of variables conspire to either worsen or alleviate the visibility of porosity. In this thorough guide, we will untangle the science behind porosity, exploring its impacts on weld high quality and unveiling advanced techniques for its control. Join us on this journey through the microcosm of welding imperfections, where accuracy satisfies understanding in the search of perfect welds.
Understanding Porosity in Welding
FIRST SENTENCE:
Evaluation of porosity in welding discloses vital insights into the honesty and high quality of the weld joint. Porosity, characterized by the existence of cavities or voids within the weld steel, is an usual worry in welding processes. These spaces, if not appropriately attended to, can compromise the architectural stability and mechanical residential properties of the weld, causing possible failures in the finished product.
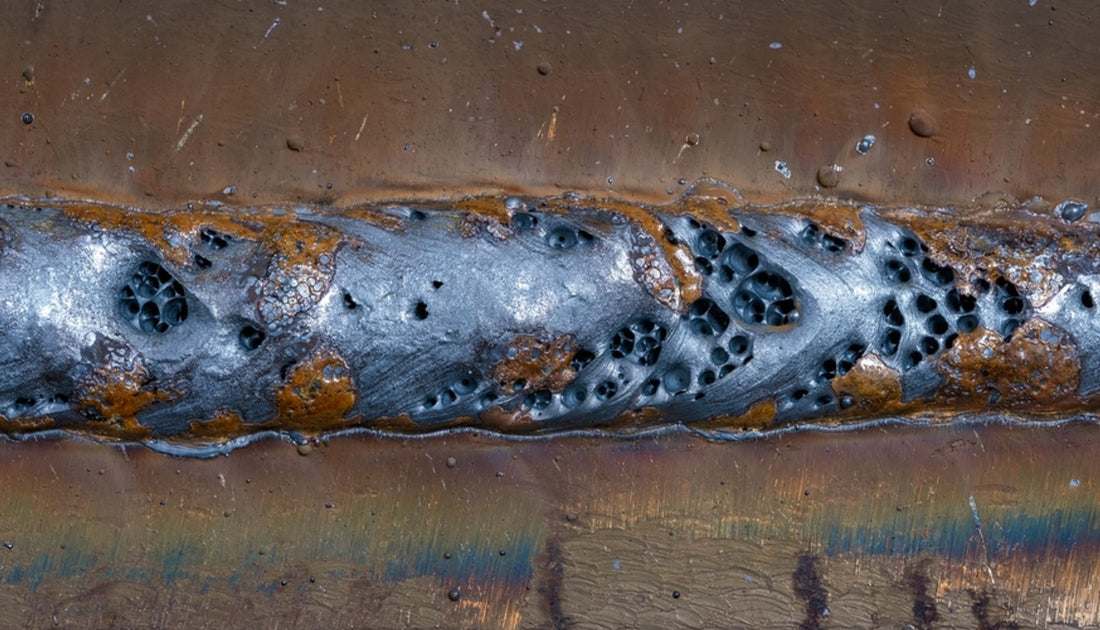
To detect and quantify porosity, non-destructive testing techniques such as ultrasonic testing or X-ray evaluation are commonly used. These strategies enable the recognition of inner issues without jeopardizing the honesty of the weld. By examining the dimension, form, and circulation of porosity within a weld, welders can make enlightened choices to boost their welding procedures and attain sounder weld joints.

Variables Affecting Porosity Development
The incident of porosity in welding is affected by a myriad of aspects, ranging from gas protecting effectiveness to the ins and outs of welding parameter setups. Welding parameters, consisting of voltage, current, take a trip rate, and electrode type, additionally effect porosity formation. The welding method used, such as gas metal arc welding (GMAW) or secured metal arc welding (SMAW), can influence porosity development due to variants in warm circulation and gas coverage - What is Porosity.
Impacts of Porosity on Weld Top Quality
Porosity formation dramatically compromises the structural honesty and mechanical buildings of welded joints. When porosity exists in a weld, it develops voids or tooth cavities within the product, reducing the total toughness of the joint. These spaces work as tension focus points, making the weld much more vulnerable to splitting and failing under load. The presence of porosity likewise damages the weld's resistance to corrosion, as the trapped air or gases within the spaces can respond with the surrounding setting, leading to deterioration over time. Additionally, porosity can hinder the weld's capability to stand up to stress or influence, more jeopardizing the general quality and reliability of the welded structure. In vital applications such as aerospace, More Help vehicle, or architectural constructions, where safety and longevity are extremely important, the detrimental effects of porosity on weld quality can have extreme effects, stressing the relevance of minimizing porosity through correct welding methods and treatments.
Methods to Minimize Porosity
Furthermore, making use of the appropriate welding specifications, such as the correct voltage, present, and take a trip rate, is critical in avoiding porosity. Preserving a constant arc size and angle throughout welding additionally helps reduce the possibility of porosity.

Using the suitable welding technique, such as back-stepping or using a weaving movement, can also aid disperse warm uniformly and reduce the opportunities of porosity development. By executing these techniques, welders can successfully reduce porosity and create top notch welded joints.

Advanced Solutions for Porosity Control
Executing sophisticated modern technologies and innovative techniques plays an essential role in accomplishing premium control over porosity in welding processes. In addition, employing innovative welding methods such as pulsed MIG welding or customized atmosphere welding can likewise assist mitigate porosity issues.
One more innovative solution includes using sophisticated welding devices. As an example, making use of equipment with built-in functions like waveform control and sophisticated power sources can improve weld top quality and lower porosity risks. The implementation of automated welding systems with precise control over parameters can significantly lessen porosity flaws.
In addition, hop over to these guys including innovative monitoring and inspection technologies such as real-time X-ray imaging or automated ultrasonic screening can aid in discovering porosity early in the welding process, enabling for instant restorative actions. In general, integrating these advanced solutions can significantly improve porosity control and enhance the total quality of bonded parts.
Final Thought
In final thought, understanding the science behind porosity in welding is click site essential for welders and fabricators to create high-quality welds - What is Porosity. Advanced remedies for porosity control can further boost the welding process and make sure a solid and reputable weld.
Report this page